ISER complies with the requirements of the ISO 9001:2008 international quality standard and is registered through QMI-SAI Global, a leading North American management systems registrar.
The intent of the Quality Assurance Plan is to achieve customer satisfaction by preventing nonconformity at all stages from design, production operations and servicing. With the implementation of ISO 9001:2008, the scope has been enhanced to include a focus on continual improvement and the assurance of conformity to customer and applicable regulatory requirements.
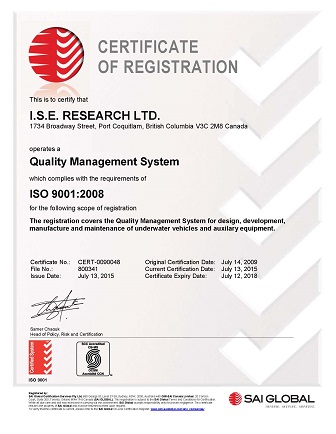
|
|
The QA plan requires a dedication to quality by all employees at all levels, who have the authority and responsibility to ensure that any non-conformance is prevented from being moved forward in production or delivered to a customer until it has been satisfactorily addressed and corrected.
Project Records are maintained to provide 'Objective Quality Evidence' (OQE) of conformance to specified requirements and the effective implementation of the quality system. Quality records from suppliers also form part of this data process. All materials and components arriving at the receiving area are directed to Quality Control (QC) for �inspection/testing�. QC is also responsible for the maintenance and calibration of inspection test equipment and the status of material during fabrication. Accepted items are tagged and released to the project for issue to the shop and assembly. Non-conforming materials are isolated and a Non-conformance Report (NCR) is raised for processing and subsequent resolution.
Validation testing is performed to ensure that the products conform to defined customer needs and requirements. New product concept design validation is generally addressed using existing testbed vehicles. Various prototype sub-systems may be manufactured and fitted to testbed vehicles to validate their performance in simulated operating conditions. With a developed product, final validation occurs during trials before delivery to the customer.
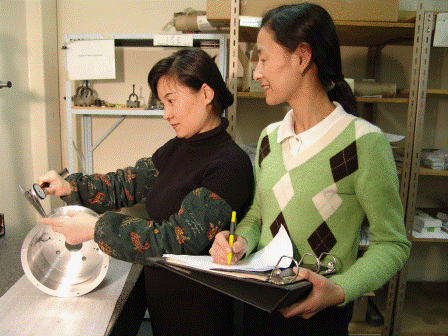
|
|
|